Sustainability in Action Feature #2: ABB’s New Berlin Plant
- Leah Gearhart
- Mar 20
- 3 min read
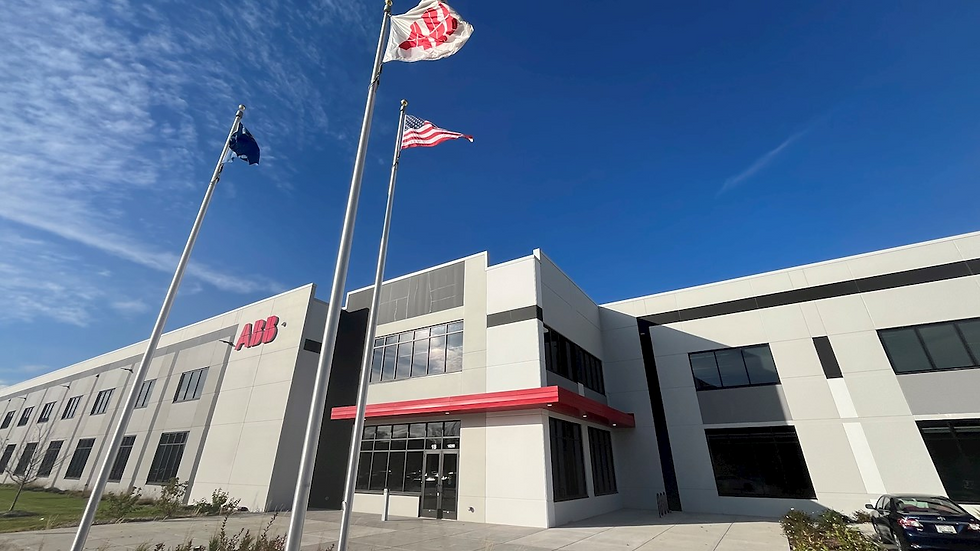
Global automation company ABB’s new 500,000-square-foot manufacturing plant in our neighboring state of Wisconsin is another game-changing changing vision for the future of sustainable manufacturing. With over 700 employees and plans for expansion, ABB is working toward a bold net-zero goal. From geothermal heating systems and smart manufacturing technologies to working towards net-zero carbon emissions, this plant is a true pioneer in integrating sustainability with innovation.
Let’s dive into what makes this facility so remarkable.
ABB’s Roadmap to Net-Zero Carbon Emissions

Geothermal heat pump installation. Photo credit: Control Engineering
At the heart of ABB’s strategy is the goal of achieving net-zero carbon emissions. This bold goal requires a comprehensive approach that permeates every aspect of the plant’s design, construction, and operations. Here are some of the key strategies ABB is employing:
Energy efficiency at scale: ABB is incorporating cutting-edge systems, like geothermal heating and cooling, that use 78 vertical wells to tap into deep-earth heat, providing both heating and cooling with minimal environmental impact. This helps reduce the plant’s energy consumption and reliance on traditional, fossil fuel-based systems.
Energy-generating infrastructure: The plant integrates solar energy and other renewable energy sources to ensure a greener power supply, directly contributing to ABB’s goal of net-zero emissions. Solar panels were strategically installed across the facility, helping offset traditional energy consumption.
Smart energy management: Using Variable Frequency Drives (VFDs) and advanced control systems, ABB optimizes energy use in real time. VFDs adjust motor speeds based on real-time demand, dynamically saving energy by reducing unnecessary power usage.
Sustainable materials: The building materials, like eco-friendly insulation and low-carbon concrete, were chosen for sustainability, reducing carbon emissions over the building’s lifecycle.
Efficient manufacturing practices: ABB’s manufacturing practices are designed to minimize waste and energy use while maximizing output. The integration of smart technologies, energy-efficient motors, and energy monitoring systems enables ABB to continually improve energy efficiency.
ABB has noted that as they continue to refine their operations, they’ll increase their sustainability practices even further, pushing the plant closer to its goal of net-zero carbon emissions.
Smart Manufacturing Methods at ABB’s New Berlin Plant:
In addition to its net-zero strategy, the New Berlin facility is a hub for smart manufacturing, an important component in achieving sustainability and operational efficiency. We’re excited to use some of these same tools in our future facility. Here’s a look at the smart technologies ABB is using:
Smart building integration: ABB’s six-screen operator workstation tracks energy usage across the entire facility. This real-time data allows the team to monitor and optimize every corner of the operation, maximizing energy savings.
AI and automation: Advanced AI-powered systems and automation are utilized to streamline production, minimize waste, and improve manufacturing efficiency.
Predictive maintenance: ABB uses predictive analytics to anticipate equipment failures before they happen, reducing downtime and ensuring that the plant runs smoothly.
Digital twin technology: The facility utilizes Digital Twin technology, creating virtual simulations of physical systems to optimize plant operations. This allows ABB to make data-driven decisions and forecast potential issues before they arise.
Energy-efficient robotics: ABB integrates energy-efficient robotics into its manufacturing processes. These robots perform tasks with precision and minimal energy consumption, reducing the carbon footprint of the plant’s operations.
Real-time data analysis: The use of real-time data analytics allows the plant to continuously monitor and optimize energy use, production efficiency, and operational performance.
Decentralized production: ABB has designed the New Berlin facility to allow for decentralized production, where smaller, localized systems work together as part of a broader, more efficient network. This reduces the need for large-scale centralized operations, cutting down on transportation emissions and improving overall energy efficiency.
A Facility Built for Growth and Sustainability
The New Berlin plant is more than just a sustainability pioneer—it’s also a key driver of economic growth. The facility will employ over 700 workers, with plans to expand by an additional 100 jobs within three years as part of a phased opening. They're another great example of how sustainability and job creation can go hand-in-hand, providing long-term value for both the community and the environment.
The Future of Manufacturing: Sustainable, Smart, and Net-Zero
ABB’s New Berlin facility is a bold step toward the future of sustainable manufacturing—one where environmental goals, cutting-edge technologies, and operational efficiency go hand in hand. Their commitment to achieving net-zero carbon emissions and integrating smart manufacturing methods sets a powerful example for manufacturers everywhere.
Furthermore, their phased opening and expansion exemplify how sustainability can be built into a growing business. As you scale your own operations, you can prioritize sustainability from the ground up, aiming for your growth to align with your environmental goals.
Resources:
Comentarios