The Hidden Costs of Peak Energy Demand (and How to Avoid Them)
- Leah Gearhart
- Mar 17
- 3 min read
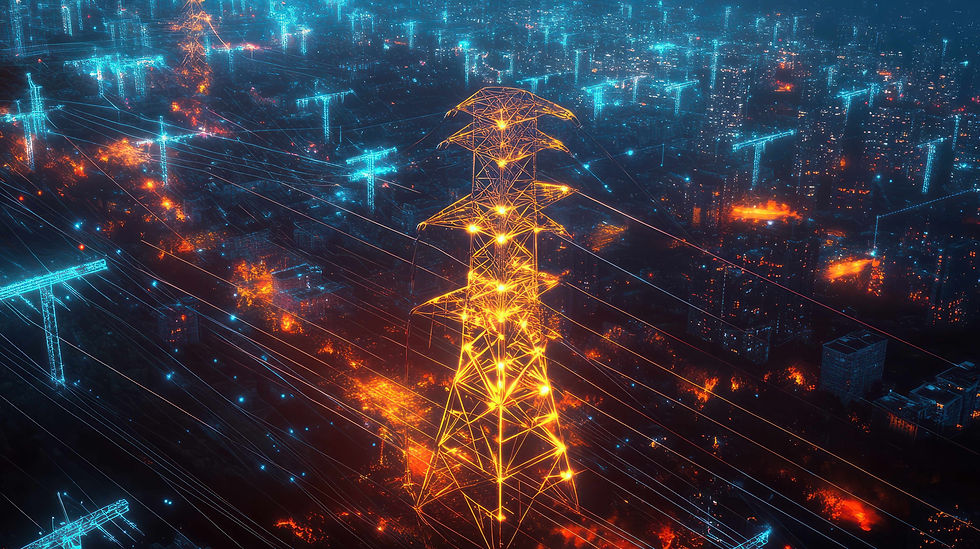
For manufacturing facilities or really any larger building, energy costs aren't just about how much power you use—it's about when you use it. Many businesses overlook the impact of peak energy demand charges, which can drive up electricity costs significantly. At our new facility, we're designing a system that doesn't just reduce overall energy consumption but strategically manages when and how power is used. By doing so, we're avoiding unnecessary expenses and improving long-term efficiency.
Understanding Peak Demand Costs
Most commercial and industrial energy bills include a charge for peak demand—measured as the highest amount of electricity drawn over a short period, often in 15-minute increments. This is the period when the most electricity is being used, typically between 2:00 PM and 7:00 PM, and utilities like ComEd set these charges based on the maximum energy used during these high-demand windows. Even if your average energy use is low, a single spike in demand during these periods can result in monthly fees that far exceed your base consumption costs.

These peak charges can add up to $1,000–$1,500 per month for our operations. A key challenge for manufacturing is that many processes require multiple high-powered systems—motors, air compressors, and cooling equipment—running simultaneously. Without intervention, these energy spikes are unavoidable. That's why we're implementing a design that flattens these peaks and optimizes energy use.
How We're Managing Demand to Cut Costs
Our approach to energy management includes three key strategies:
1. Leveraging Solar Power to Reduce Midday Demand
Solar energy production aligns well with peak pricing periods, particularly in the summer. By installing solar panels, we can offset a portion of our energy use during the most expensive times of the day. This not only cuts our reliance on the grid but also prevents large spikes in power usage that would trigger higher demand charges.
2. Using Ice Storage for Smarter Cooling
Cooling systems account for a significant portion of industrial energy use, and running chillers during peak hours is a major contributor to demand spikes. Instead of relying solely on traditional air conditioning, our facility will use an ice storage system. Here's how it works:
At night, when electricity rates are lower, our system will produce ice and store it in large insulated tanks.
During the day, rather than running energy-intensive chillers, the system will use the stored ice to cool the building.
This reduces energy consumption precisely when utility rates are at their highest, lowering overall demand charges.
This concept is already in use at large-scale cooling plants, such as Thermal Chicago's system that serves downtown skyscrapers, including Willis Tower. By integrating it into our facility, we're adopting a proven strategy for demand management at an industrial scale.
3. Incorporating Battery Storage for Peak Load Shaving
Battery storage is another tool we're implementing to smooth out demand peaks. When energy demand starts rising, batteries can provide supplemental power rather than drawing directly from the grid. This allows us to maintain stable energy consumption levels even when multiple systems are running.
Additionally, battery storage positions us to take advantage of Demand Response Programs—incentives offered by utilities to businesses that agree to temporarily reduce power usage during times of grid strain. With automation and predictive energy management systems, we can participate in these programs without disrupting operations, creating another cost-saving opportunity.
The Long-Term Benefits of Smart Energy Design
Beyond immediate cost savings, our approach to peak demand management offers long-term benefits:
More predictable operating costs by minimizing exposure to fluctuating energy prices.
A reduced environmental footprint by minimizing the need for costly, high emission peaker plants and increasing reliance on renewable energy sources like solar and wind.
Scalability for growth—our facility is designed with flexibility in mind, so future expansion won't mean exponentially higher energy costs.
In Illinois, energy sources like nuclear, solar, and wind provide a steady baseline of power. However, during periods of high energy demand—such as hot summer afternoons—utilities often turn to "peaker plants" to meet the surge. These plants, typically powered by natural gas or coal, are older and more expensive to operate due to high fuel costs and maintenance requirements. They also have a higher environmental impact compared to baseline energy sources. The energy generated during peak demand is both more expensive and more polluting, which is why managing peak demand is critical for cost reduction and environmental sustainability.
By implementing our energy strategies—like solar panels, ice storage, and battery integration—we are reducing our reliance on these costly and environmentally harmful peaker plants. This helps to lower both our operational costs and the environmental impact of our facility, contributing to a more sustainable and resilient energy system.
More to Come!
We’re excited to share more about the specific systems we plan to implement, including our solar panel array, ice storage system, and battery integration. As we move closer to operation, we’ll also be sharing real-time data that will provide valuable insights into our energy management strategies and their effectiveness.
Comentários